Slowly but Surely: Follow the Kaizen Method of Continual Improvement
Aug 05, 2019
5 mins
CN
Fondatrice de Dea Dia
“Patience and the fullness of time do more than force or fury.”
The moral of Aesop’s fable, The Lion and the Mouse, unknowingly demonstrates a Kaizen state of mind, a Japanese approach to productivity based on the idea that small, daily improvements lead to major changes. Kaizen was formulated in Japanese companies, but it’s a philosophy that could apply not only to company culture, but to all of us in our personal lives, to help us achieve our goals.
The methodology was created in the 1950s in Toyota factories in Japan and has since spread all over the world.
What is Kaizen?
The word “Kaizen” is a contraction of two Japanese terms:
Kai - change
Zen - better
Kaizen is a process of incremental growth based on small, repeated daily improvements. For this to work, it must involve all team members who must each offer their ideas for growth. The idea is to focus every day on eliminating problems and optimizing the work process. It’s a gentle, progressive method, the opposite of “disruption” or “revolution”, which involve much more brutal changes.
“A journey of a thousand miles begins with a single step”—Lao Tzu
Kaizen is more than just a simple management technique: it’s a state of mind. Every project should be viewed as “a journey of a thousand miles”. A long distance can look overwhelming if you want to cover it too quickly, but all it takes is to break it down into smaller steps and you’ll go the distance without any major issues and achieve your final goal. With this system, you get there slowly but surely.
Why favor slowness?
Small, repetitive changes are more efficient than one single, radical transformation. Our brains are wary of drastic changes, which it views as potential danger and thus rejects them. To create change, it’s better to break down an ambitious objective into smaller, easier-to-accomplish tasks that are less likely to trigger our infamous resistance to change and—on the contrary—can even inspire pride, pleasure, and encouragement.
Take the example of someone who wants to start running again after years without any exercise. Imagine what would happen if they wanted to run a marathon on day one. They would suffer a lot for a pitiful result and become disillusioned. However, if they set a running goal each day that is slightly more ambitious than the last, they would more easily be able to run a marathon after a few months.
A bit of history
Kaizen was created in Japan in the 1950s to facilitate the rebuilding of Japanese industry after the Second World War.
The technique was initiated at Toyota by Taiichi Ohno as part of lean management, a more comprehensive principle that seeks to increase a company’s production quality by following a procedure of continual improvement.
Masaaki Imai is the man credited with making the Kaizen system famous in the West. Born in 1930, he worked for the Japanese Productivity Center in America in the 1950s, which was created to improve Japanese productivity after the war. It was through this work that he ended up meeting Ohno in the 1960s. Later, in 1985, he founded Kaizen Institute to help companies to adopt the Kaizen method as well as offer all the tools that go by the name of lean management today.
The main principles
In his books, Masaaki Imai shares a few basic principles of the Kaizen system:
- Constantly question yourself: Even if something is working, it can always be improved. It’s the only way to stay competitive.
- Don’t seek perfection but continual improvement: Perfection will be achieved by the repetition of small, daily improvements.
- Identify the original cause of problems to solve them in a sustainable way: Simply dealing with the symptoms of a problem without looking for the root leaves the door open for the problem to happen again.
- Solve problems straight away: It’s important to deal with problems as soon as they occur, before they get worse and it becomes more complicated and costly in terms of time and energy to fix them.
- Put changes in rank order: It’s better to prioritize putting in place quick, easy and cheap solutions.
- Involve all the members of a team in the search for solutions: Each employee, no matter where they are the hierarchy, must feel free to express themselves, suggest ideas, participate, and commit to any suggested changes.
5 Kaizen techniques that are easy to apply
The Kaizen system relies on several methods and techniques to achieve its goal of continual improvement:
1 - The 5S Method
The goal of this method is to improve our workspace and our well-being (or that of the team) to increase efficiency, waste less time and energy, reduce the risk of accidents, and ultimately improve production quality.
The 5 S come from five Japanese words:
- Seiri: sorting, creating a lighter work space
- Seiton: tidying, optimizing the work space
- Seiso: cleaning the work space
- Seiketsu: arranging, anticipating dirtiness and mess
- Shitsuke: being rigorous, encouraging self-discipline
2 - The PDCA cycle or the Deming Wheel
This four-step plan allows for quick testing and adjusting of products or processes until the expected result is achieved, all in a reduced amount of time. To do this, there are four actions to follow:
- Plan
- Do
- Check
- Adjust
This creates a virtuous circle within the company that allows for several changes while verifying that they have had a positive impact and adapting to them. This is the operating mode in any Agile approach.
3 - The 5 Whys Method
This deals with one of the main principles of the Kaizen method according to Masaaki Imai: getting to the source of problems in order to find a sustainable solution. To do this, you must ask “why?” five times.
Example: my work site is running behind schedule.
Why? Because one of the contractors didn’t meet the deadline.
Why? Because he didn’t have the necessary materials.
Why? Because they weren’t delivered in time.
Why? Because they were ordered late.
Why? Because the person in charge of purchases was away and didn’t have a replacement.
The contractor who didn’t meet the deadline isn’t to blame for the delay, a lack of staff is the reason behind it.
4 - Retrospectives
Rituals like stand-up, taken from the Agile approach, are often used in Kaizen systems. During the ritual, teams meet up and form a circle to provide updates on production by using Post-Its to visualize each person’s tasks. Each team member must express themselves and speak about the project they are working on. They must talk about their successes and also the problems they are facing so that the team, as a group, can help solve them.
5 - Kanban
This visual flow management tool reduces production delays and improves team reactivity. The method is visual and easily understood by everyone, based on a just-in-time method: the information is provided to the team members in a timely fashion so they aren’t overwhelmed with useless information.
Two principles to respect in the company
The Kaizen method should not become a way of pressuring teams or it loses all meaning. To be used efficiently, all the while respecting employee well-being, certain main principles must be respected.
Everyone is involved
All the employees of a company must bring in changes, wherever their place within the hierarchy. This inclusion is one of the guiding principles of Kaizen. Everyone must suggest ideas, agree with the proposed changes, and take part in them. This implies respect, trust, and open-mindedness from managers.
Implementing an incentive program
A company’s success is its employee’s success. It’s important to prove it by showing recognition when deserved and rewarding each team member through an incentive program. This can take many different forms; what’s important is that it remains fair and impartial.
Respecting these main principles will help to implement a system of continual improvement that optimizes productivity, product or service quality, as well as pleasant working conditions, and translates into a real and sincere investment from all employees.
Translated by Kalin Linsberg
Photo: WTTJ
Follow Welcome to the Jungle on Facebook and sign up for our newsletter to receive our articles every week
More inspiration: Productivity & tools
Goal setting: How to bounce back when you feel like a failure
The big F word ... Failure. We all face it, but here’s how to make it your secret weapon for success.
Dec 18, 2024
Productivity boost: Why mental health outshines long hours
Long hours don’t equal better work. Discover how mental health support can unlock productivity and time efficiency in the workplace.
Nov 28, 2024
10 fun ways people are using AI at work
While many use AI for basic tasks like grammar checks or voice assistants, others are finding innovative ways to spice up their work days.
Nov 05, 2024
12 Slack habits that drive us crazy
Slack is a top messaging platform, but coworkers can misuse it. Over-tagging and endless messages can make it frustrating ...
Oct 16, 2024
10 CareerTok creators you should be following
Looking for career advice? CareerTok has quick tips from real experts on interviews and job offers.
Sep 25, 2024
The newsletter that does the job
Want to keep up with the latest articles? Twice a week you can receive stories, jobs, and tips in your inbox.
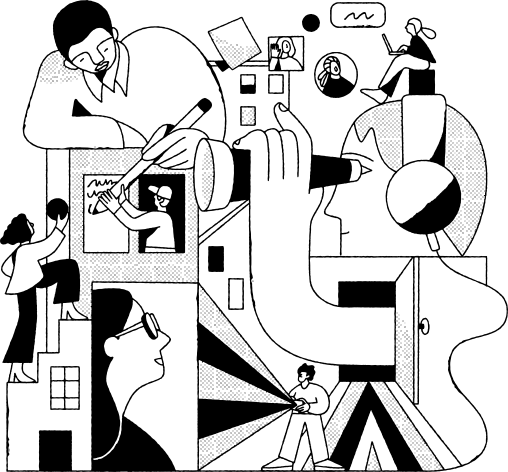
Looking for your next job?
Over 200,000 people have found a job with Welcome to the Jungle.
Explore jobs